Offset printing is a widely used printing technique where the inked image is transferred from a plate to a rubber blanket, then to the printing surface. Also known as offset lithography, this method is renowned for producing high-quality prints in large quantities.
It is the preferred technology for a range of products such as newspapers, magazines, brochures, and books.
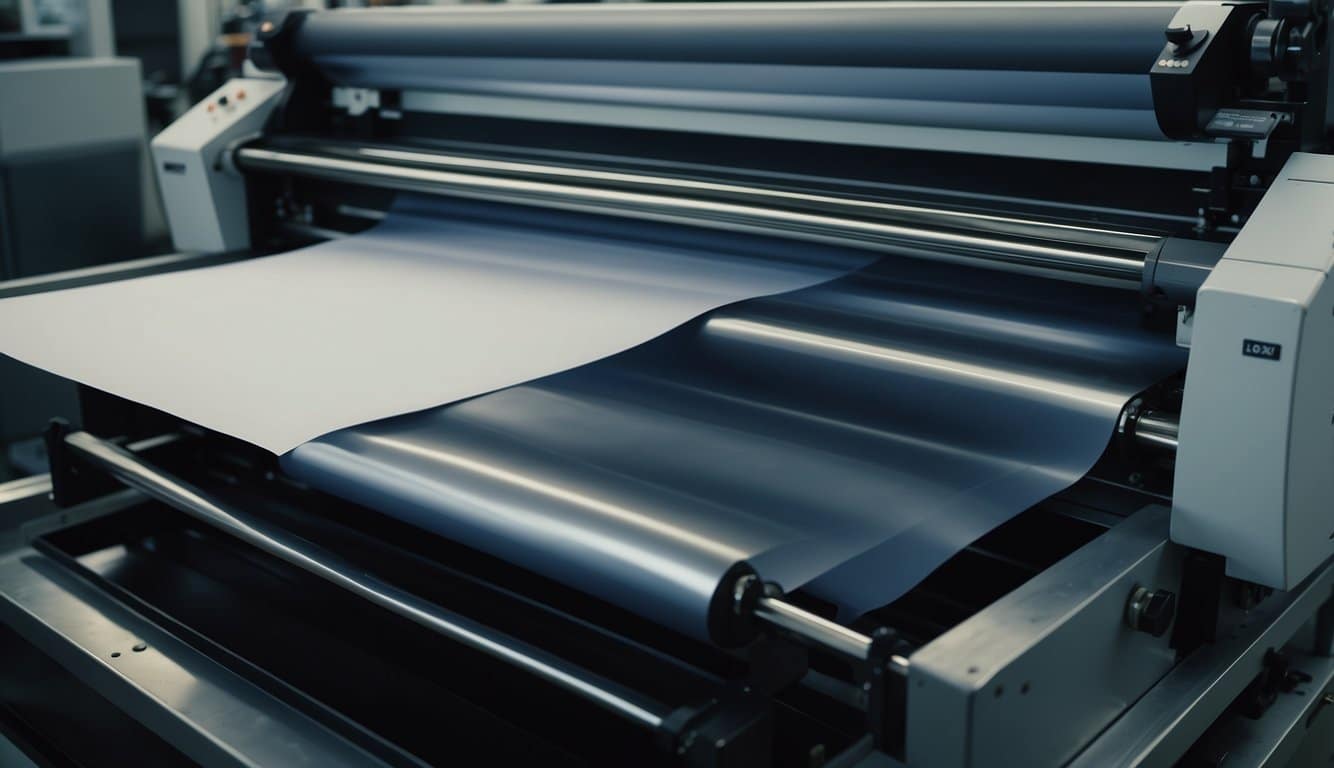
The process dates back to the early 20th century, evolving from stone lithography, and has since undergone significant technological advancements. Today’s offset presses are automated and efficient, capable of printing on various materials with remarkable consistency and speed.
Understanding the basic principles of offset printing is not only essential for anyone involved in the print production industry, but also crucially for small business owners and marketers who need to understand what type of local printing company you may need for your job.
Key Takeaways
- Offset printing is a primary method for producing high-volume, high-quality prints.
- Technological advancements have made offset presses more automated and versatile.
- This printing technique works on a wide range of materials and offers consistent quality.
History of Offset Printing
Offset printing emerged as a significant evolution in the print industry, marking a departure from earlier printing methods and setting a new standard for efficiency and quality.
Inventions and Innovations
Offset printing, a form of lithography, was developed in the early 20th century. It utilizes a flat image carrier where the image to be printed obtains ink from ink rollers, while the non-printing area attracts a water-based film, keeping the non-printing areas ink-free.
A pivotal innovation came from American inventor Ira Washington Rubel in 1904. Rubel accidentally discovered that printing from the rubber blanket of a printing press delivered a clearer image than printing directly from metal plates.
Subsequently, in 1906, Robert Barclay from England devised the process for offset printing on tin, adapting the methodology of transferring an image onto a rubber blanket from paper to metal. This facilitated the use of offset printing in a new realm—packaging. The core principle developed by these innovations is the indirect image transfer that offset printing is known for, allowing for cleaner and more precise prints.
Notable Figures in Development
One of the key personalities in the development of offset printing was Ira Washington Rubel. He was responsible for the serendipitous innovation that fundamentally shaped offset printing. Rubel’s work contributed extensively to the swift acceptance and refinement of this technology in the early stages.
Robert Barclay also played a vital role as he recognized the potential of offset printing beyond paper and ushered it into packaging. This broadened the scope of offset printing, which proved to be far-reaching and influential.
Basic Principles of Offset Printing
In offset printing, your images are transferred from plates to a rubber blanket and then onto the printing surface. This indirect (i.e. “offset”) approach is key to the precision and quality of the final product.
Lithographic Process
The foundation of offset printing is the lithographic process. This process relies on the fundamental principle that oil and water do not mix. Before printing begins, your printing plate—typically made of aluminum—gets treatment so that the image area is receptive to oil-based ink and the non-image area attracts water.
During the print run, the plate is dampened, first with water then with ink. The water adheres to the non-image areas, while the ink sticks to the image areas.
Image Transference
The core of offset printing lies in the image transference stage. Here’s how it unfolds:
- Transfer from Plate to Rubber Blanket: The inked image from the printing plate is first transferred to a rubber blanket. This step is crucial because the rubber blanket can conform to the texture of the printing surface, allowing for a more accurate and consistent image.
- Transfer to Printing Surface: The image on the rubber blanket is then pressed onto your chosen printing surface, be it paper, card, or another material. This step is performed by the impression cylinder of the press and is a gentle yet precise process that ensures the fidelity of the inked image until the final transfer is complete.
The ink in offset printing is specifically formulated to provide a balance of color, drying speed, and adhesion. The rubber blanket’s job is not only to transfer ink but to do so uniformly while ensuring that the non-image areas remain ink-free.
The precision of the process means that you obtain a clear, sharp, and high-quality print every time.
Offset Printing Technologies
In the realm of offset printing technologies, you encounter sophisticated systems designed to improve efficiency and print quality. These systems have drastically evolved, integrating advanced computerized mechanisms.
Computer-to-Plate Systems
Computer-to-plate (CTP) systems have revolutionized the prepress stage by directly transferring your digital images onto printing plates. This process bypasses the need for traditional film, which streamlines your workflow and reduces the potential for error. The highlights of CTP include:
- Accuracy: Ensures that images are transferred to plates with fine precision.
- Speed: Significantly reduces the prepress time, leading to faster turnaround.
Inking and Dampening Systems
The inking system is responsible for uniformly applying ink to the printing plate. The inking system consists of:
- Distribution Rollers: Ensure the ink is evenly spread across the plate.
- Form Rollers: Transfer ink to the image areas of the printing plate.
The dampening system applies a fountain solution to the non-image areas of the plate to repel ink. It consists of:
- Fountain Solution: A mixture of water and other chemicals that prepares the non-image areas to repel ink.
- Dampening Rollers: They apply the fountain solution to the plate.
These two systems work in tandem to maintain the balance between ink and water on the plate, which is critical for producing clear, sharp images on the printed material.
Offset Printing Press Components
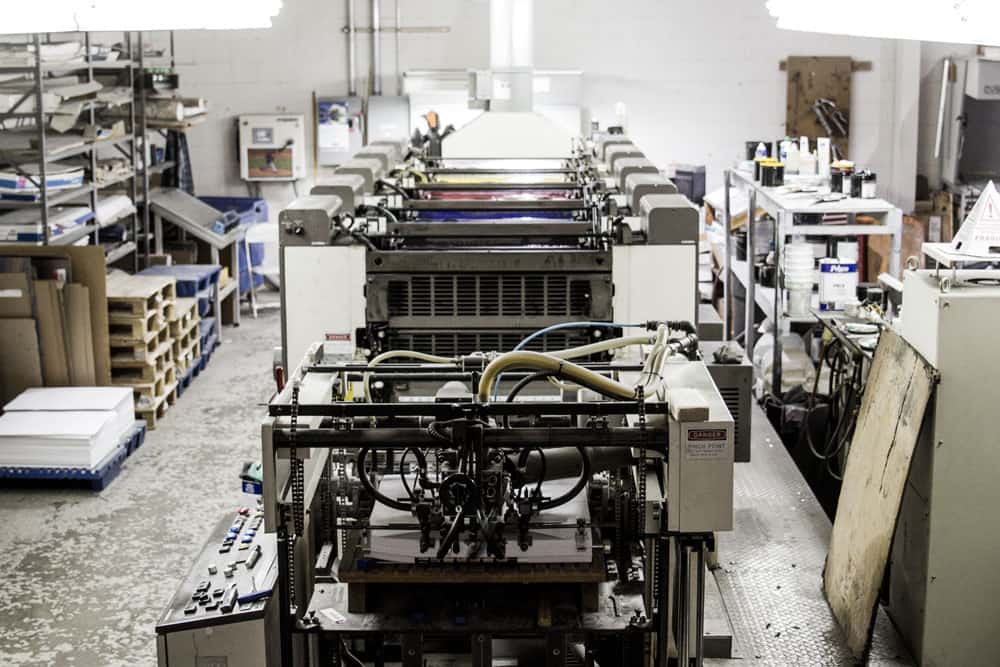
In offset printing, the press components are crucial for transferring the image from the printing plate to the substrate. Each component has a distinct role that ensures precision and quality.
Plate Cylinder
The plate cylinder is a core component where the image is first applied. The printing plate, typically a thin sheet of aluminum, wraps around this cylinder. It carries the image that you want to print and is crucial for transferring the image onto the blanket cylinder.
Blanket Cylinder
The blanket cylinder receives the image from the plate cylinder. This cylinder is covered with a rubber blanket that compresses to transfer the image to the paper. It acts as an intermediary to ensure a clean and even application of the image.
Impression Cylinder
The impression cylinder applies pressure against the blanket cylinder to transfer the image onto the paper. Your substrate (typically paper but synthetic substrates and packaging are also quite often the material of choice) passes between the blanket and impression cylinders, where the print is made.
Ink Rollers
Ink rollers distribute ink to the printing plate. These rollers must deliver a precise amount of ink to the plate cylinder to maintain consistency across prints.
- Ductor roller: Moves between the ink fountain and the ink rollers, controlling the amount of ink applied.
- Distributor rollers: Ensure even ink distribution by spinning against each other.
- Form rollers: Transfer ink directly to the plate cylinder. The number of form rollers can affect the ink coverage and sharpness of the image.
Water Rollers
The water rollers apply a water-based fountain solution to the non-image areas of the plate cylinder. It is critical that the balance between water and ink is maintained to prevent smudging and to achieve high print quality.
- Fountain roller: Picks up the fountain solution from the water pan.
- Metering rollers: Regulate the amount of water distributed to the rest of the rollers.
Prepress and Plate Making
The prepress stage is where we prepare documents for the printing process. This phase is crucial, as it ensures that your files are correctly formatted and that all graphical elements are in place for a high-quality print. Here are the key components of the prepress process:
- File Preparation: Your files must be print-ready, often in a PDF format. Ensure all fonts, images, and colors are properly embedded, and all files are saved at print resolution (300 dpi).
- Proofing: Digital proofs are generated to preview the final print. This is your chance to review and make any necessary corrections. Physical proofs can be had for a small price, and while press proofs used to be more common, they can be very expensive if you find something you don’t love and are typically reserved for the most discerning of consumers willing to pay a price for perfection.
Prepress Step | Description |
---|---|
File Submission | Submit print-ready files in the required format. |
Preflight | Check for errors such as missing fonts or graphics. |
Color Management | Ensure color accuracy across all devices. |
Proofing | Create a digital or physical proof for review. |
When your prepress production is complete, we’ll proceed to plate making. This involves transferring your digital images onto physical printing plates.
- Image Carrier Creation: A printing plate, usually aluminum, is coated with a photosensitive layer.
- Exposure: Your digital image is transferred onto the plate using a computer-to-plate (CTP) system, where lasers etch the image.
- Development: The plate is developed to wash away non-image areas. The remaining image areas are ink-receptive.
CTPlate Making Steps:
- Coating: Apply a photosensitive layer to the plate.
- Exposure: Use lasers to etch the image from your digital file onto the plate.
- Development: Treat the plate to reveal the ink-receptive image areas.
Your success in offset printing is highly dependent on the precision and quality control maintained during these prepress and plate-making processes.
Types of Offset Printing
Offset printing is a widely used printing technique that comes in various types to accommodate different print volumes and page sizes. Each type offers unique advantages depending on your project’s requirements.
Sheet-Fed Offset Printing
With sheet-fed offset printing, individual sheets of paper are fed into the printing press. This method is ideal for small to medium print runs, and you’ll find it provides flexibility with a wide range of paper sizes and types. Sheetfed offset presses can handle high-quality print jobs like brochures, business cards, and other customized products.
Web Offset Printing
Web offset printing is a continuous process where a large roll of paper is fed through the press. It’s cut into sheets after printing, which makes it efficient for high-volume jobs like newspapers and magazines. You will notice two primary versions:
- Coldset Web Offset: Uses ink that dries through absorption and evaporation, suitable for uncoated paper stock.
- Heatset Web Offset: Utilizes drying lamps to cure the ink, perfect for coated paper stock and achieving a higher-quality finish.
Dry Offset
Unlike traditional offset printing that uses wet ink and transfers it to a rubber blanket before printing, dry offset uses a process where the ink is directly transferred to the final surface without any water. This approach is mostly used for printing on non-porous materials like plastics and metals. Its quick drying time increases production speed, making it a good choice for packaging materials.
Materials and Substrates
The choice of materials and substrates is crucial in offset printing as it affects print quality, durability, and compatibility with the press. You need to select suitable paper or aluminum plates based on your specific job requirements.
Paper
Paper is a primary substrate for offset printing, and its characteristics significantly impact the final print. Choose the appropriate weight, coating, and texture to match your project’s needs:
- Weight: Heavier papers are more durable and impart a feeling of quality, whereas lighter papers are economical and suitable for high-volume printing jobs.
- Coating: A coated paper, either gloss or matte (a.k.a. silk), provides a smoother surface, ensuring sharper image quality. Uncoated paper offers a natural, tactile feel, ideal for writing or ecologically-minded organizations looking for recycled options.
- Texture: The texture of the paper can range from smooth to linen or felt. This choice should align with the aesthetic goals of your print job.
Remember, the paper’s absorbency and finish will influence ink usage (which can affect price significantly on longer runs) and the overall look of the printed piece.
Aluminum Plates
An aluminum plate is essential in the offset printing process and serves as the carrier of the image to be printed.
- Durability: Aluminum plates are highly durable and can withstand the stress of the printing press, making them suitable for large runs.
- Surface Treatment: The plates must be grained to ensure proper ink adhesion and water retention during printing.
An investment in high-quality aluminum plates with precise surface treatment helps guarantee consistent results throughout the print run.
Color Systems and Techniques
In offset printing, the reproduction of full-color images is typically achieved through two main color systems: CMYK and ink matching systems. Understanding these systems is crucial for achieving accurate and consistent colors in your print projects.
CMYK
CMYK stands for Cyan, Magenta, Yellow, and Key (Black)—the four ink colors used in the offset printing process. This system is also known as four-color process printing. When you mix these colors in varying degrees, they produce a wide spectrum of colors. For instance:
- Cyan (C) is used in combination with other colors to create blue and green shades.
- Magenta (M) mixes with yellow to make reds and with cyan to produce purples.
- Yellow (Y) is essential for creating greens when mixed with cyan and oranges when combined with magenta.
- Black (K), also referred to as the “key” color, adds depth and detail to an image.
The typical CMYK color model is represented in percentage values for each color, with 0% meaning no ink and 100% representing full saturation. Here’s an example in a table format:
Color | Cyan | Magenta | Yellow | Black |
---|---|---|---|---|
Sample | 100% | 50% | 0% | 0% |
Ink Matching Systems
Ink matching systems are used to ensure color consistency across different print runs and materials. One widely adopted system is the Pantone Matching System (PMS).
This system provides a standardized color reproduction framework that allows you to specify exact colors using designated Pantone numbers. For instance, if you need a specific shade of blue for your brand logo, you would provide the Pantone code to ensure the color is accurately reproduced each time it is printed.
PMS color matching is not as popular as it once was, however. Computer screens don’t allow the precise control over color that exists in print, and the widespread availability and affordability of four color printing, especially with digital print engines, means brands have been forced to become less picky about exact color matches.
Other systems, such as Toyo and Focoltone, also exist to serve similar purposes, however they are not as widely adopted as PMS and you may have trouble finding a local offset printing company that uses them.
These systems play a critical role when precise color matching is necessary, and the standard CMYK process cannot replicate a specific color faithfully.
Each matching system has its own set of unique colors and associated codes, which are essential for your print provider to precisely render the colors you have specified for your project.
Offset Printing in the Digital Age
Offset printing has embraced digital technologies, resulting in enhanced efficiency and new capabilities. You will find a synergy between traditional offset and digital printing, particularly in the realms of digital printing integration and variable data printing.
Digital Printing Integration
Digital Offset: Some manufacturers have started using the term “digital offset printing” referring to offset presses that incorporate high levels of automation. However, this is all marketing speak and offset printing is still offset printing.
There are, however, some digital printing processes that attempt to mimic the offset printing process. The most widespread of these is the HP Indigo line which uses an “ElectroInk” which is a toner that is transferred to a blanket cylinder before being applied to the print medium.
Digital printing has come a long way and is a great option for shorter runs, but still cannot match offset printing for efficiency on longer runs.
While they may not be able to replace offset presses, by adding and incorporating digital systems, offset printing operations are able to put your job (or even parts of a job) on the equipment that is best suited to your needs.
Inkjet and toner technologies have been incorporated into offset processes as well, offering you the flexibility to switch between digital and offset printing within the same workflow.
Inkjet Technology:
- Used mainly for small runs or specialized material.
- Allows for in-line finishing and variable data incorporation.
Toner-based Systems:
- Ideal for combining with traditional offset for high-quality, short runs.
- Environmentally friendly due to no need for chemical plate processing.
Variable Data Printing
Digital printing, especially inkjet, has revolutionized personalized marketing by enabling Variable Data Printing (VDP). This technology allows you to customize each piece of printed material, such as adding a recipient’s name or a unique code, without slowing down the printing process.
Applications of VDP:
- Personalized direct mail campaigns.
- Customized brochures and marketing materials.
Benefits of VDP:
- Higher response rates due to personalization.
- Better customer engagement and tracking capabilities.
By integrating digital printing technologies with offset printing, you gain unparalleled flexibility, efficiency, and the potential for customization that the digital age demands.
Offset Printing Applications
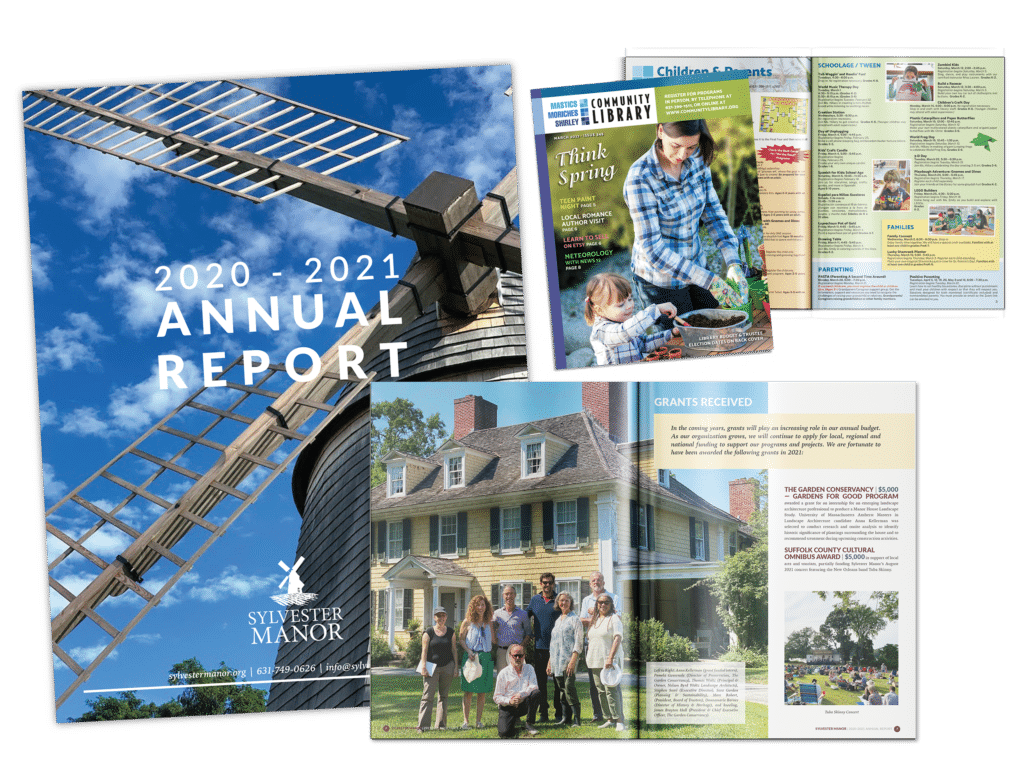
Offset printing (offset lithography) is versatile enough to accommodate a vast spectrum of applications. This printing technique ensures high-quality, consistent image reproduction and is economically viable for long runs.
Packaging
Your products’ packaging often serves as the first interaction between your brand and prospective customers. Offset printing plays a crucial role in this sector, providing high-resolution graphics for boxes and cartons.
This method can handle a range of packaging materials and styles, from simple product labels to intricate packaging designs.
- Material Compatibility: Works with a variety of substrates, from paper to cardboard.
- Print Quality: Delivers crisp, clear images and type, which is essential in label and packaging design.
Magazines & Newspapers
For the publication of magazines and newspapers, offset printing is the go-to process because of its efficiency and clarity. It allows publishers to reproduce sharp texts and images, a key requirement for the high-volume print runs these publications demand.
- Color Reproduction: Superior, with consistent, vibrant colors.
- Speed: Rapid production times for meeting the pressing deadlines of periodicals.
Commercial Printing
In the realm of commercial printing, your marketing materials‘ appeal can benefit greatly from offset printing’s precision and cost-effectiveness. This encompasses a broad range of products, including brochures, flyers, and stationery that showcase a professional look and feel.
- Economies of Scale: More cost-effective with increased quantities.
- Versatility: Able to print on various paper types and finishes, enhancing the tactile experience.
Quality and Production Advantages
Offset printing offers you distinct quality and production benefits, which encompass high-grade image quality and consistent results over long print runs.
Image Quality
Offset printing produces superior image quality with fine detail and color fidelity. The use of plates allows for sharp, clean images and type without streaks or spots that are sometimes seen in other types of prints.
Color control is precise, with potential to utilize a wide range of inks and Pantone colors to match your specific color requirements.
- Fine detail reproduction: You can achieve exceptional detail and fine lines.
- Color fidelity: The printed colors are vibrant and closely match the original design.
Consistency and Reproducibility
Your projects benefit from the unparalleled consistency and reproducibility that offset printing brings. Once the initial setup is complete, every print is a near-clone of the first.
- Uniformity: Your entire print run maintains the same quality from the first piece to the last.
- Reproducibility: Should you need more prints later, the results will be consistent with your initial batch, assuming the same paper and inks are used.
By choosing offset printing, you can confidently rely on high-quality, consistent print outputs that are ideal for large-scale production needs.
Economic Factors
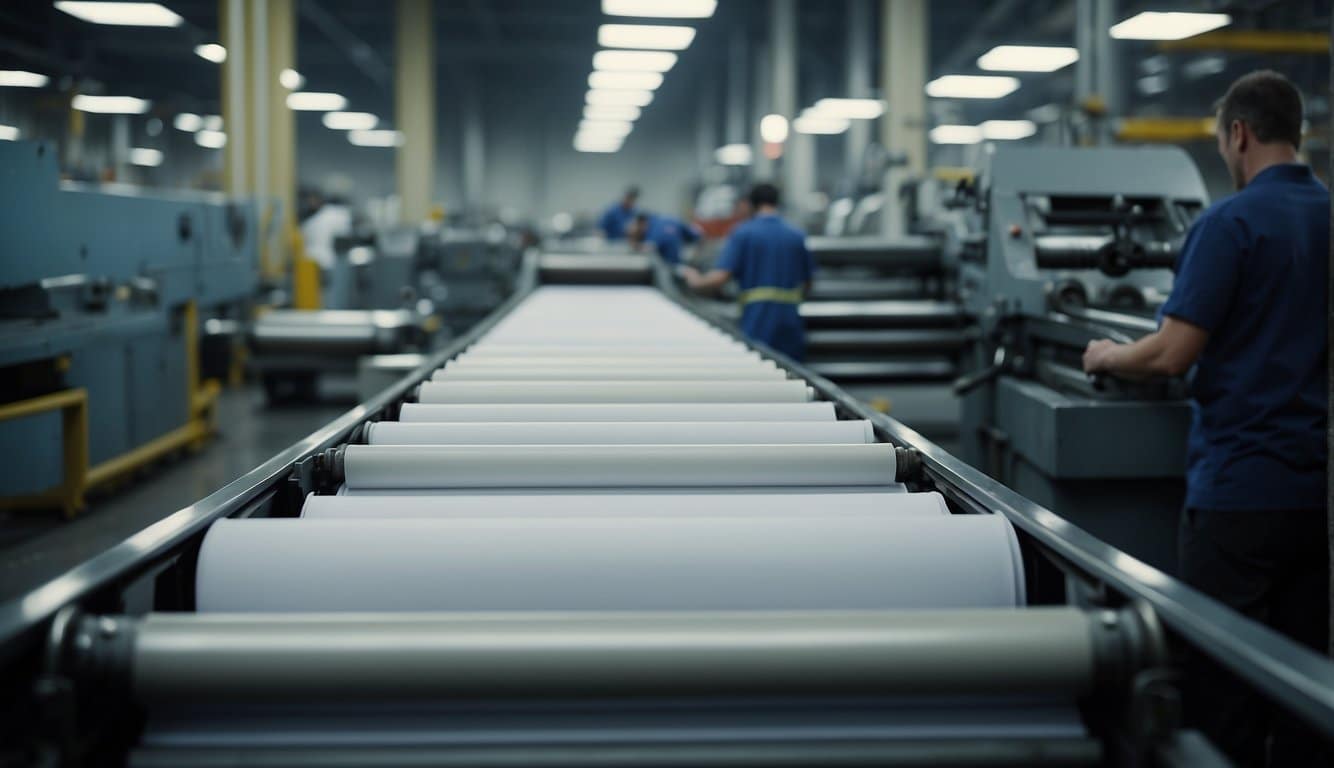
When considering offset printing, you must be aware of the economic factors that impact your project’s cost-effectiveness. These include initial setup costs and the turnaround time associated with your print job.
Setup Costs
The initial setup costs for offset printing are notably higher than for other printing methods. This is due to the need for creating plates for each image. For short runs, this upfront investment can make each copy more expensive.
- Plate creation: A one-time cost, approximately $75 to $100 per plate.
- Quantity: Larger quantities distribute the setup cost, reducing the price per unit.
Offset printing becomes economical with longer runs, as the per-unit cost decreases significantly when you spread the fixed setup fees over a large number of prints.
Turnaround Time
Offset printing’s turnaround time is impacted by the preparation and drying time required.
- Preparation: Prepress tasks, including plate creation, can take one to two days.
- Drying time: Inks may need 12 to 24 hours to dry, requiring additional time before finishing processes.
You should plan your print jobs accordingly, keeping in mind that rush orders can significantly increase costs. Offset is ideal when you have the flexibility for longer lead times, ultimately benefiting from its cost efficiency for high-volume orders.
Comparative Analysis
In this section, we’ll explore the differences between offset printing and digital printing, as well as the distinct benefits and drawbacks associated with offset printing. This comparative analysis will help you better understand which printing method suits your needs.
Offset Printing vs. Digital Printing
Offset printing is a traditional method where images are transferred from plates to rubber blankets, then onto the print media. Conversely, digital printing directly applies the image onto the media using toners or liquid ink.
- Speed and Volume: Offset printing is slower to set up but is efficient for large runs, whereas digital printing offers a quicker turnaround for short runs.
Cost Efficiency:
- Offset: Cost-effective for larger quantities due to economies of scale.
- Digital: More cost-effective for small to medium runs due to minimal setup costs but higher running costs.
- Color Accuracy and Consistency: Offset printing excels in uniformity and color fidelity across high-volume jobs. Digital printing provides good color reproduction but may vary slightly throughout a run. While both processes can produce excellent results, offset allows for much more precise adjustments than digital printing.
- Customization: Digital printing allows for easy customization or variable data printing, which isn’t as feasible with offset printing.
- Print Quality: Offset printing generally provides higher resolution images and cleaner, finer lines. Digital prints are high quality too but results can vary greatly depending on the machine.
Pros and Cons – The Benefits and Drawbacks of Offset Printing
When evaluating offset printing, you’ll find a range of benefits and drawbacks that may influence your decision-making process.
Pros – Advantages of Offset Printing:
- Quality: Produces sharp, clean images and type with high image fidelity.
- Materials: Versatile with a wide range of printing surfaces including paper, synthetics, cloth, metal, leather, and textured paper.
- Ink Control: More precise ink and water balance, contributing to superior image quality.
- Economical: Unit cost decreases as the quantity increases, making it ideal for large runs.
Cons – Drawbacks of Offset Printing:
- Setup Time: Requires more time to create plates and set up the press, leading to longer lead times.
- Cost: Although economical for large volumes, the initial setup costs can be high, making it inefficient for small runs.
- Flexibility: Less flexible for short turnaround times and last-minute changes compared to digital printing.
- Waste: More waste is produced in terms of preparation and test sheets, impacting environmental considerations.
Comparing offset to digital printing involves assessing your project’s scale, cost considerations, quality expectations, and time constraints to make an informed decision.
Frequently Asked Questions
In this section, you’ll find concise answers to common questions about offset printing, helping you understand its uses, benefits, and advancements.
What is the difference between digital and offset printing?
Offset printing involves transferring ink from a plate to a rubber blanket, then to the printing surface. Digital printing, on the other hand, uses toners or liquid ink, applying color directly onto the material without plates. Offset is preferable for high volume and quality, while digital is better for lower quantities and variable data.
What are the primary advantages of using offset printing?
Offset printing’s advantages are its exceptional print quality and cost-effectiveness for large runs. The more you print, the lower the cost per page because the initial setup costs are distributed across the quantity being produced.
What applications is offset printing most suitable for?
You’ll find offset printing ideal for a wide range of applications, especially when you require high-quality prints in large volumes. This includes packaging, newspapers, books, magazines, catalogs, packaging, brochures, and stationery.
How does sheet-fed offset printing differ from other types?
Sheet-fed offset printing presses print on individual sheets of paper that are fed into the machine. It’s contrasted with web-offset printing, which uses large rolls of paper and is typically used for high-volume publications like newspapers.
What are the latest advancements in offset printing technology?
Recent advancements in offset printing include computer-to-plate (CTP) systems, improved automation for faster setup and turnaround, better inking and dampening systems that enhance print quality and reduce waste, and camera-based monitoring systems that are capable of making automated adjustments to print runs on the fly.
How has offset printing sustained its relevance in the current digital age?
Despite the digital shift, offset printing has maintained relevance through continuous innovation, high-quality output, and its ability to handle large-scale print jobs cost-effectively. Its integration with digital techniques has also allowed for greater flexibility in print solutions.